If you’ve spent any time working on firearms, you undoubtedly know that springs are the lifeblood of any gun. Springs are essential to the operation of any firearm. Even one spring not functioning properly is enough to bring your firearm to a complete halt. In most cases, restoring or repairing a firearm involves replacing springs.
However, repairing or restoring a firearm often entails trying to find springs long out of production. While there are places that specialize in hard to find gun parts, a lot of times it seems like the particular spring you’re looking for is out of stock(quite possibly permanently) or completely unavailable. When that happens, we’re left with a couple of choices: shelf the project until one turns up or make the spring ourselves. Today, I’m going to demonstrate how to make some of the harder springs to find: flat springs.
Flat springs used to be used very frequently in firearm design. They’re not used so often in newer designs. But they’re very common in older guns-which are often the subjects of our repair or restoration projects. The particular project I’m working on here is the repair of an old Iver Johnson top break revolver. The trigger spring was broken, preventing the trigger from properly resetting. I’m going to make this spring to illustrate the techniques for making flat springs.
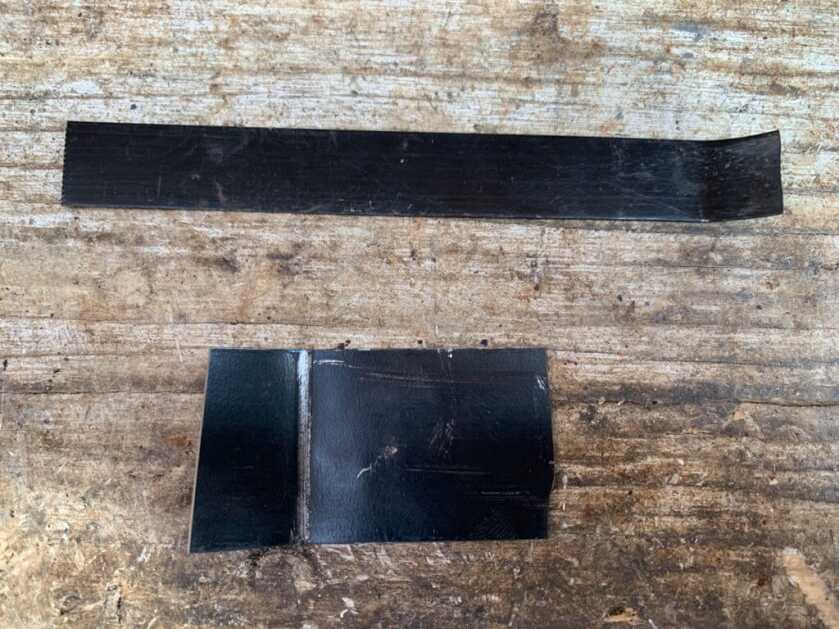
You don’t need a whole lot of equipment to make flat springs. Obviously, you need some suitable spring steel from which to make your spring. You need the appropriate tools to shape the steel into whatever spring you’re trying to reproduce. The spring I’m making for this project is fairly simple, but the same techniques work with more complex springs. You’ll need a heat source and some oil to harden the spring. I use a MAPP torch for this task, but you could probably use a propane torch (or even a campfire if you’re really desperate). For tempering the spring you can use the same heat source, but it’ll be difficult to avoid overheating the spring. It’s easier to accomplish tempering the spring using a lead pot, like what you use for casting bullets (don’t worry it won’t affect your next round of casting). That’s really about it.
Spring steel is available from a variety of different sources. The gunsmith supply houses like Brownell’s stock suitable material in different thicknesses and sizes. One source of material I use is steel banding material from freight shipments. Some of this is actually pretty good spring steel, but by no means all. For my fellow cheapskates out there, left over steel banding can often be had for nothing in places that receive a lot of freight. You just have to do the work to determine if the particular material is suitable.
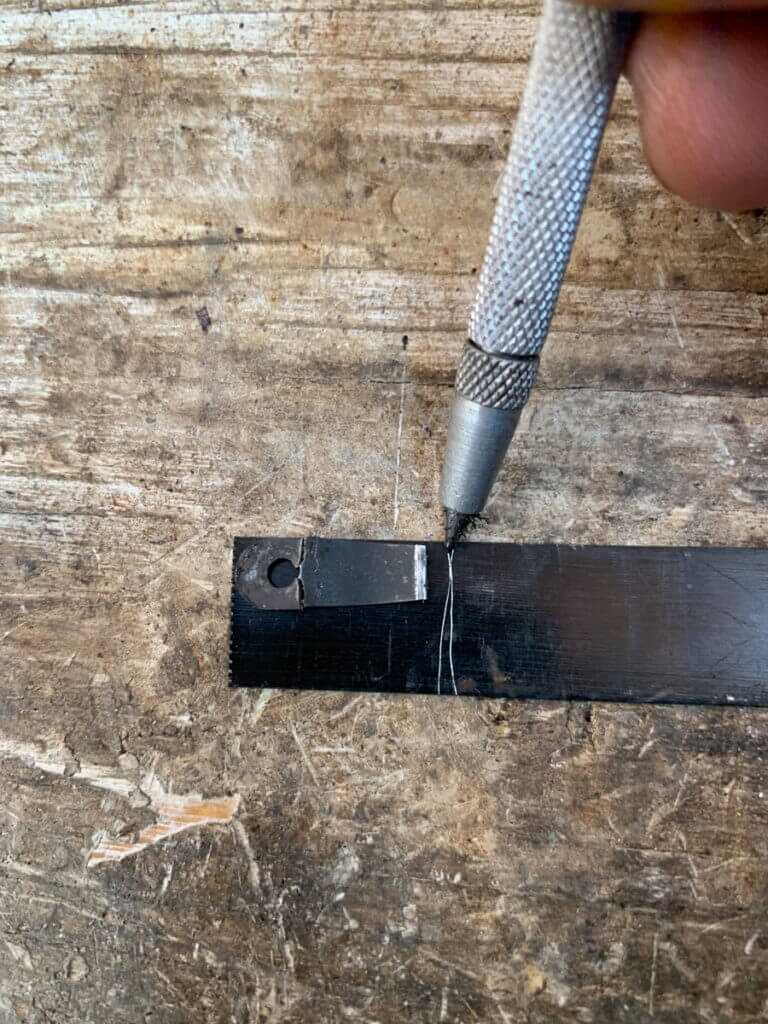
Fortunately, the old, broken spring was still in the revolver (trying to make a new spring without having a “sample” to recreate is a bit more challenging, but still possible). So I had a pattern to make the new spring. It’s sort of tear-dropped in shape with a hole and has a radius bent on one side going longways. For “roughing out” the basic shape I used a set of hand shears (aka tinsnips). I started by cutting a section of material to the length of the old spring. Then I “rough cut” the width of the spring. Since the piece was square-shaped, I cut the corners off of what would be the round end.
After cutting out the a piece of banding roughly the size of the spring, it was time to add the hole. The hole in the original spring measured right at 1/8”. Obviously a vice was not suitable to hold this thin piece of metal. So I held onto it with a set of vise grip pliers. I used a drill press and a center drill to drill the hole. But any method of drilling a hole would work for this particular spring as it’s just a clearance hole for a screw to pass through.
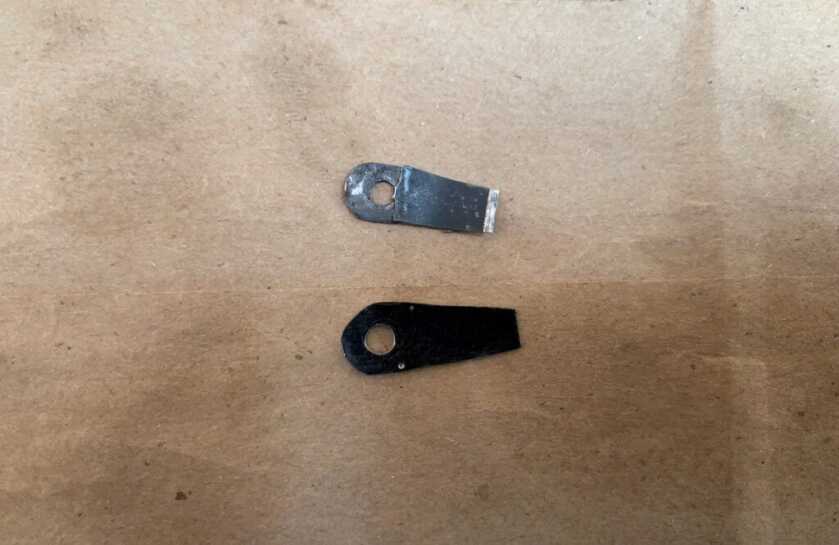
Then I cleaned up the shape of my spring. I used a belt sander for part of this and a file to do the detail work. The belt sander was really handy for reproducing the radius on the “fat” end. I did the tapered end with this as well. For the radius I found a round piece of steel lying around the shop that was pretty close to the original spring radius. I formed the new spring around it. If you don’t have random steel lying around, you can really use anything round that’s close to the size of the radius you want to bend.
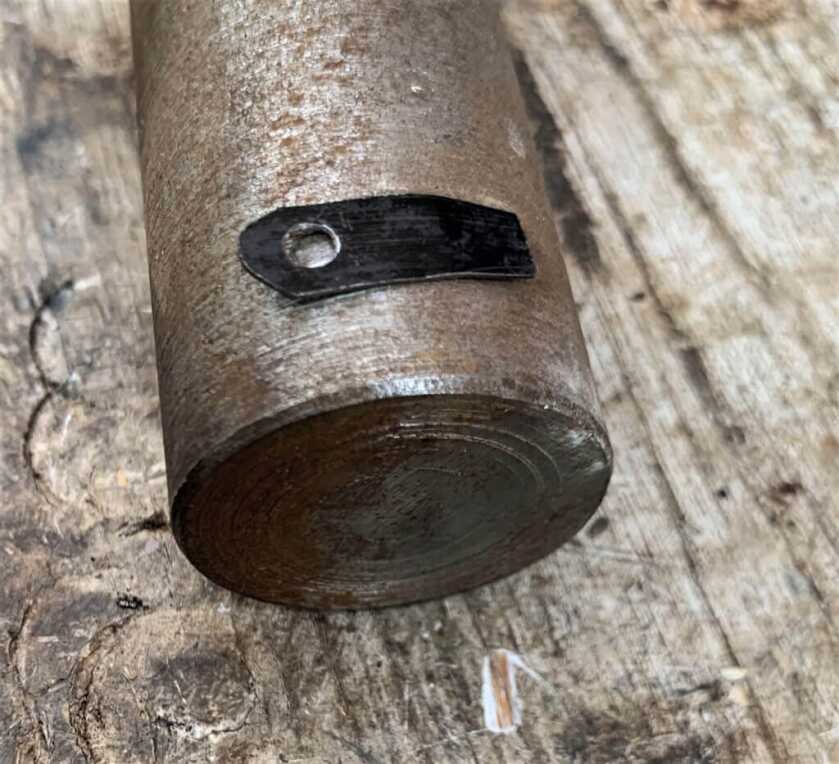
For the next part of this project, a little bit of explanation of the process is in order. Hardening steel involves heating it up to a particular temperature and then rapidly quenching it in water, oil, or whatever medium is appropriate for the specific alloy. However, the steel has to have sufficient carbon content for it to harden. Depending on the application, the hardening process frequently leaves the steel too hard-similar to a piece of glass. So the tempering process is used to “take out” some of the hardness, leaving it hard enough for its intended purpose but with enough ductility to be tough. Obviously, this is a very simplified description of the process but I think you get the idea.
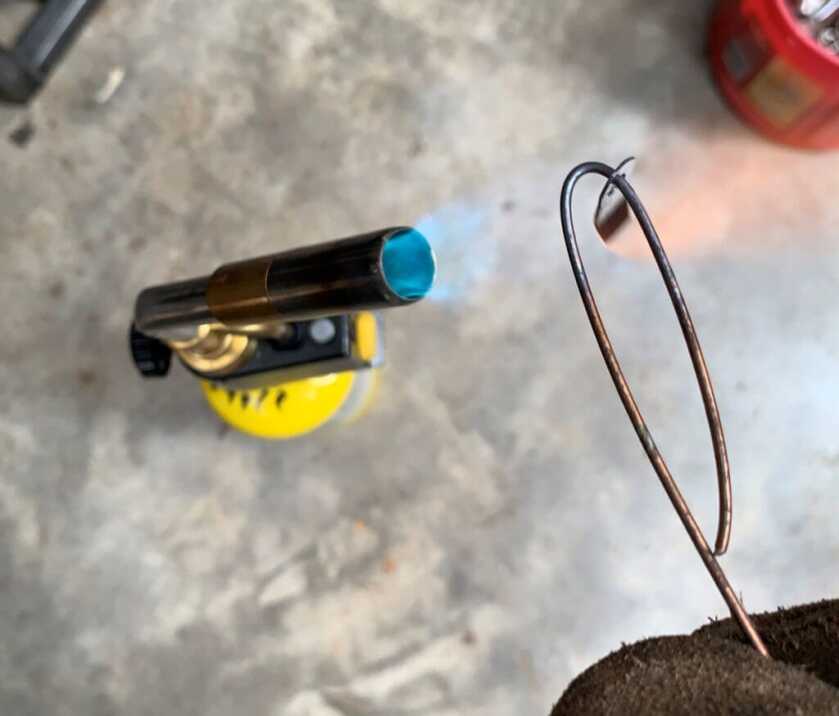
Because most of you do not own a heat-treating oven, I’m going to do this process with a “low tech” method. I used a MAPP torch to heat the steel for the hardening process. Steel changes colors at different temperatures. So you can see how hot the steel is by carefully watching its color as you heat it. The target here is for the part to be a dull red color. The spring we’re making is obviously very thin, so it heats up REALLY fast. It’s rather challenging to evenly heat it without overheating it. Once I had heated it to the proper temperature, I quenched it in oil-which is the proper quenching medium for spring steel. Keep the spring completely submerged in the oil, and swirl it around in the oil until it cools off. Then remove it and clean it off for the next step.
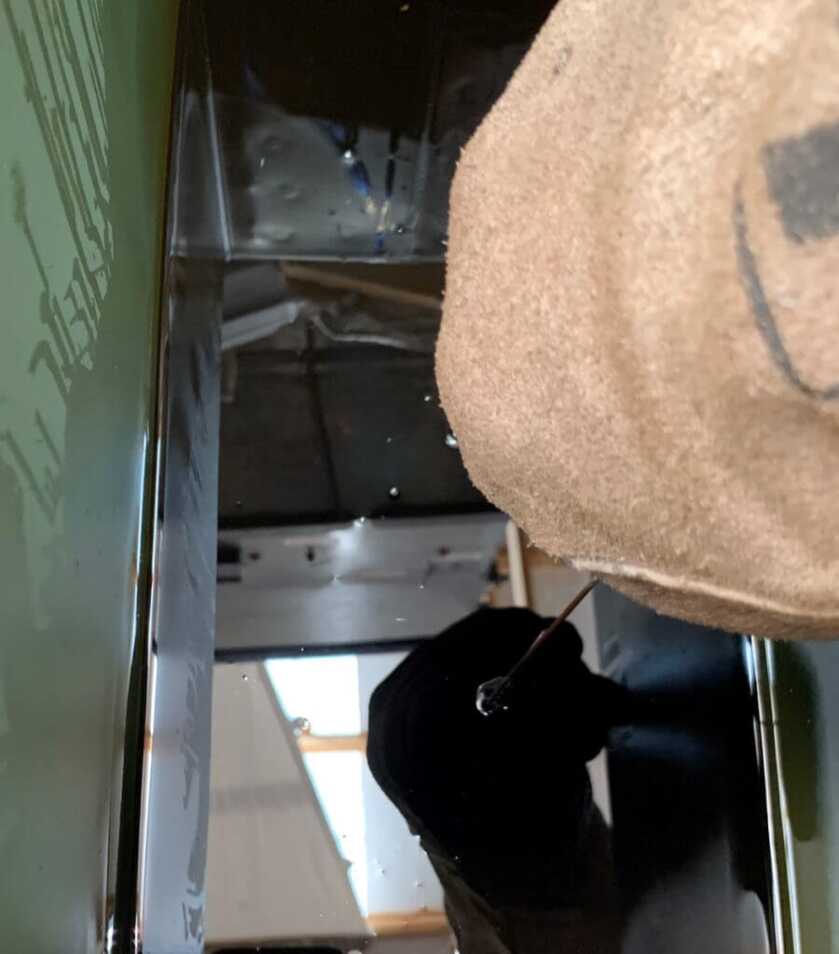
At this point, the spring is too brittle to be usable, so it needs to be tempered. Since again, most of you reading this do not have the aforementioned heat treat oven, I’m going to describe a low tech method for this as well. The steel needs to get to about 600 degrees for tempering. Again, we’re going to use the color of the steel as a guide to its temperature, which is indicated by the steel being a blue color. In order to be able to see that, the steel needs to have the black colored coating left from the oil quench scrubbed off of it.
This time the process needs to be a bit more delicate, so you probably don’t want to attempt this with a torch. If you did the hardening process I described, you might have noticed that the part heated so fast that it seemed to skip the lower temp colors and went right to the higher temps in a few seconds. If you go past the tempering temperature, you’ll take the hardness back out of the steel and you’ll need to start back over at the hardening and quenching.
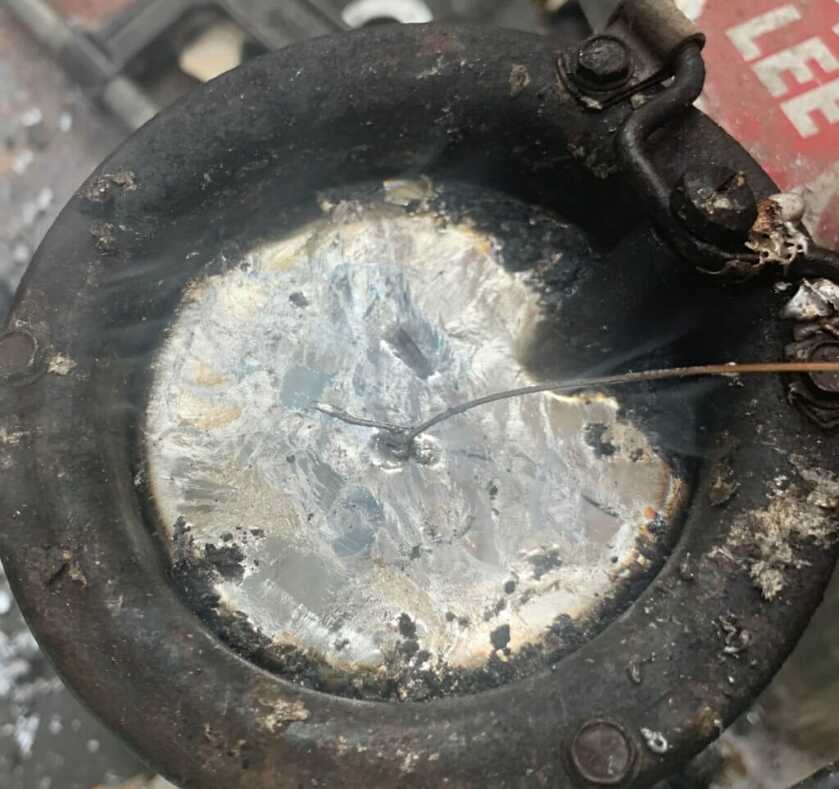
For those of you unaware, lead melts at 600 degrees, which is the temperature the steel needs to reach for tempering. So I turned on my lead pot and once it had melted the lead, I immersed the spring in the molten lead. Because of its size and thickness, the spring still heated up pretty quickly. It turned blue after probably 10-20 seconds in the lead. But it was still slow enough to be manageable. If you go past the blue color and the steel turns gray, you’ll need to start over at the hardening phase. So check your part every few seconds until it turns blue. If you’re the DIY type and cast lead bullets, then you already have the appropriate equipment to do this. But there are other ways if you don’t.

The last step in making a flat spring is to test it. The specifics of this depend on the particular spring you’re trying to make. Obviously different springs function differently. Basically the spring should compress and “spring” back. It is normal for the spring to crush a little and not spring all the way back. If the spring breaks or doesn’t spring back enough to be usable, then either the steel was not suitable or something went wrong in one of the heat treating processes.
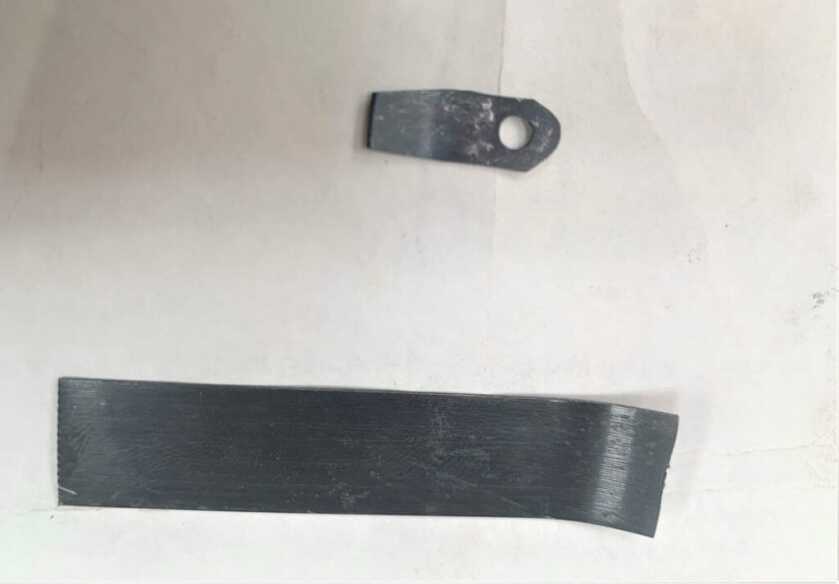
If you restore or repair older firearms, you will eventually run into a broken spring for which a replacement is unavailable. Being able to make a replacement is a very useful skill to have. If you need a replacement spring quickly, making a spring allows you to get the firearm back in working order without having to wait for a spring to be shipped to you. So before you relegate that old gun to the scrap heap because you can’t find a spring for it, take a look at making one. Until next time, Happy ‘Smithing!
I am looking to replace a very similar-looking spring as in your article above for a vintage airgun. However, it has a squarish notch cut in the end opposite the hole, leaving two “teeth” that keep a squared-off windage adjustment screw from turning. The spring acts as a lock on the windage adjustment screw on an elaborately designed peep sight. How would you cut out the square notch on the end? And would you do that before hardening and tempering it? Thanks in advance for your response.
The hand spring in Colt style single action pistols (it is the same in the black powder and the 1873s) is notoriously fragile, and even if you have a replacement it is a pain to get the stub of the old one out of the hand and secure the new one. Fortunately, because of the popularity of cowboy action shooting, replacement springs are readily available from VTI GunParts.
there’s youtube videos on brownell and midway usa channels with an old english gunsmith named jack rowe,the guy was brilliant! he shows how they made old english double barrels and how they made parts,well worth the watch!
I have repaired about 2 dozen old shotguns in the last 20 or so years. Typical for back action locks have a large flat spring that works the hammer and a small one that sets the sear. One or both are unusually broken or the temper is gone.
Dixie Gun Works sells Spring Stock in all of the usual thickness needed. For about $5.00 you can start with excellent metal in the proper thickness, The rest it up to you.
A fellow who seemed to know quite a bit about what he was talking about described to me another way of tempering a spring. He said to submerse it in most any kind of oil, then cook it off, heat the oil and spring with a torch, just a propane or Mapp torch is good enough, and heat it until all the oil burns off. I guess some experimenting would be in order.
One question that I forget to ask is do you quench the spring after tempering or just let it cool slowly? Great article, thanks.
Yes the burning oil method is another way to temper the spring. The idea there is similar in that the point of burning off the oil is just a gauge of the temperature. As long as the oil you’re burning off has an ignition temperature of 500 degrees or so, it’ll basically work the same way. And there are other mediums that you can use for this task as well.
And you want to let the spring air cool after the heating it for tempering.
Good article but I wonder why you wouldn’t drill the hole before cutting out the spring, much more material to hold while you drill it that way.
You could certainly do that as well. I found it to be a little easier to locate the hole in the order I described. But there’s “more than one way to skin a cat” so to speak.