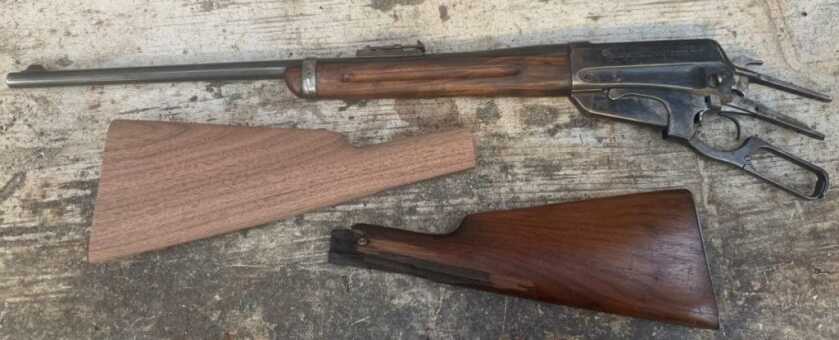
Recently, I had a rather interesting project come my way from GunsAmerica’s own True Pearce. Mr. Pearce had an original Winchester 1895 rifle, chambered in 30-40 Krag that needed a new stock fitted to it. Fitting a wood stock would seem to be something of an “old school” gunsmithing task in today’s world of synthetic stocks, drop-in parts, and buffer tube-mounted collapsible stocks. But it is surprisingly relevant to the hobby gunsmith of today. There are all sorts of projects a hobby gunsmith might wish to take on that involve fitting or finishing wood furniture. This article is meant to be an overview of the process of fitting and finishing that stock, not necessarily provide step-by-step instructions (as this would be space prohibitive). My objective is to show the hobby gunsmith that it’s within their capability to take on a project like this. At any rate, the original stock was broken out at the side of the top tang and Mr. Pearce wanted a new replacement fitted.
Most inletted replacement wood stocks are left with some fitting required. This is done to allow them to be properly fitted to the rifle. Some of this is just practicality, as older rifles like the subject of this article, had considerable variation in their dimensions, by today’s standards at least. So leaving the stock oversized allows enough “meat” on them to ensure a proper fit and good appearance. And obviously, a finish needs to be applied to the bare wood as well to protect the wood and for aesthetics. The stock used in this project came from Here
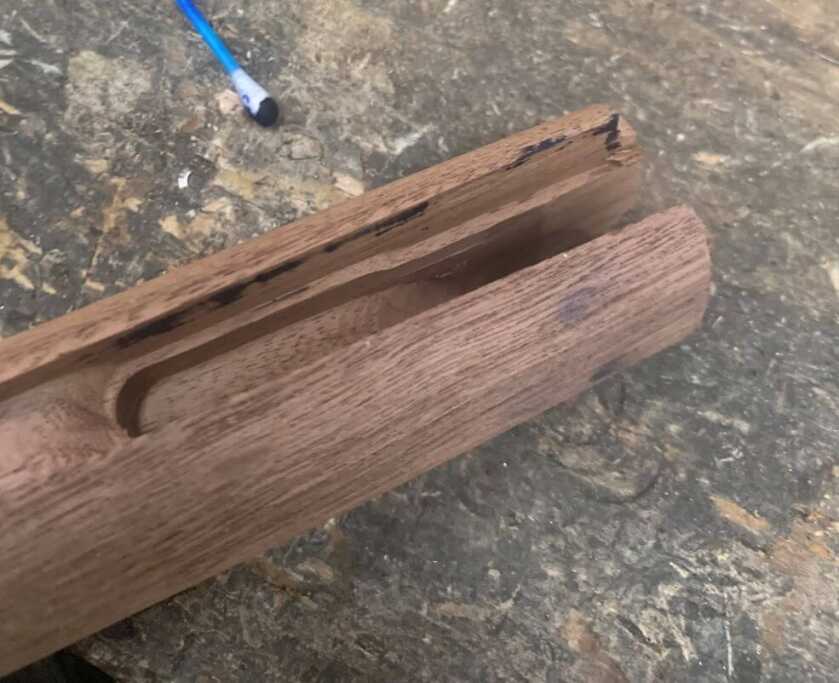
There actually aren’t all that many tools required to fit a stock. I used this
for inletting black. I used an Exacto knife for some of the internal work. I used a palm-handled gouge for the radius at the back of the tang. I used a palm-handled skew chisel for other portions. I also used a carving knife for some of the detailed material removals. I purchased these specialty woodworking tools from the carving tool section of the Woodcraft store in Franklin, TN but they’re available online here. Files are used for internal work, in addition to external shaping. I used this oil finish. Lastly, I used sandpaper of different grits for finish prep.
The first thing I needed to do was to do the internal fitting to allow the stock to slide into place. This is something of a delicate process. You don’t want to remove too much material or it will look awful at best, or at worst the improper fit will cause the stock to break prematurely. So go slow and don’t be in a hurry. Don’t use too much force trying to install it, push too hard and you’ll break the stock.
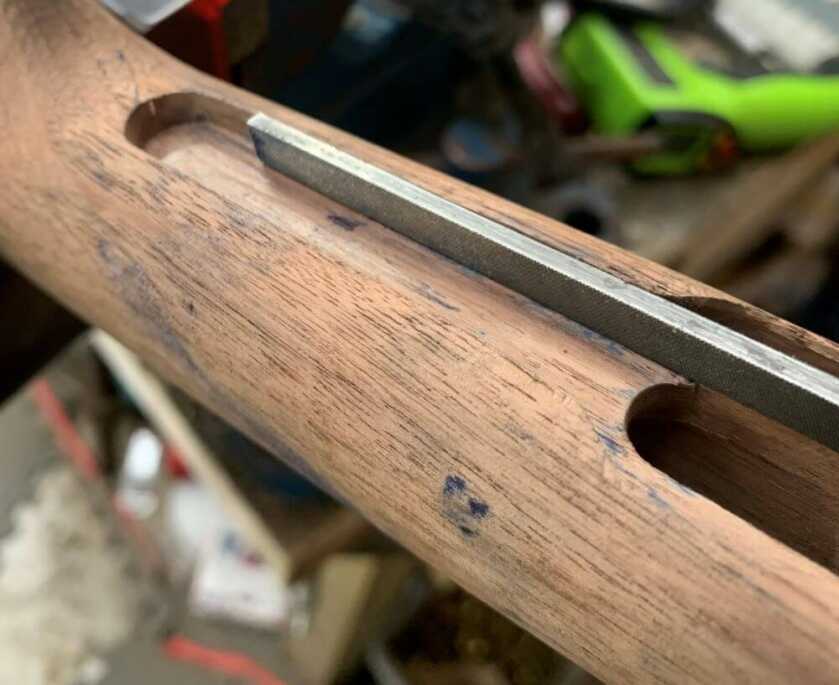
First, apply the inletting blue on the internal features of the rifle that the stock needs to fit. This will leave some on the places of the stock that are interfering, which will show where material needs to be removed. Use it sparingly, as it’s a pain to clean up and it spreads like anti-seize grease. The “dirty” appearance of the stock in the pictures is proof of this. At any rate, the inletting blue will transfer some onto the areas that are interfering with the stock, giving you a visual indication of where you need to work.
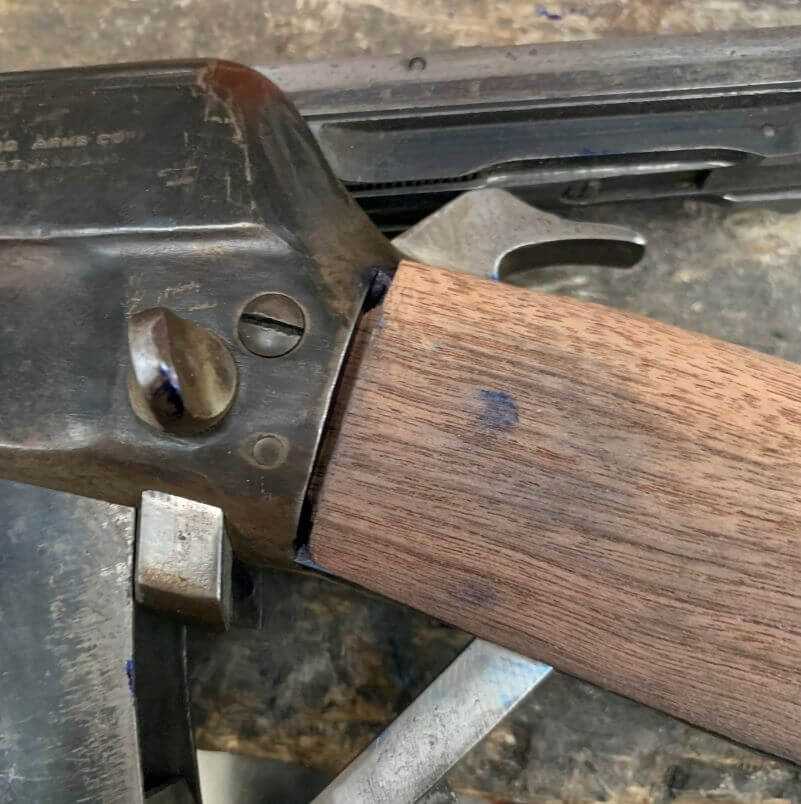
There are a lot of internal features that have to be fitted with this model of Winchester. Some wood-stocked rifles are considerably simpler in this regard. So I couldn’t just focus on one area, rather I had to work around all of the internal features a little at a time. I used all of the cutting tools and files I mentioned earlier at different points of this internal work. You keep working at the high spots all around until the stock slides in like it should and you have even contact all the way around. Go slow and take just a little at a time. It’s a lot easier to take wood off than it is to put it back again! Lastly, I removed the inletting blue from the rifle and the stock.
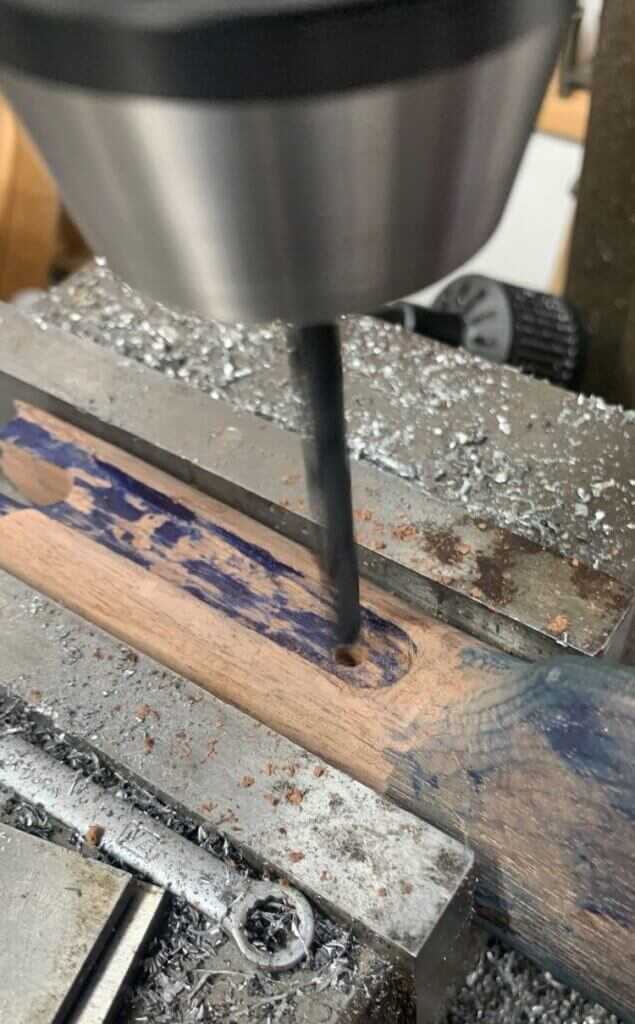
With the internal fitting complete, I needed to drill the hole for the tang screw. This was pretty straightforward. I marked the hole, and then put the stock in the milling machine to drill the hole. I did this before I started with the external work. So if I managed to put a mark on the stock in the process, I’d remove it in the process of external shaping and finish prep.
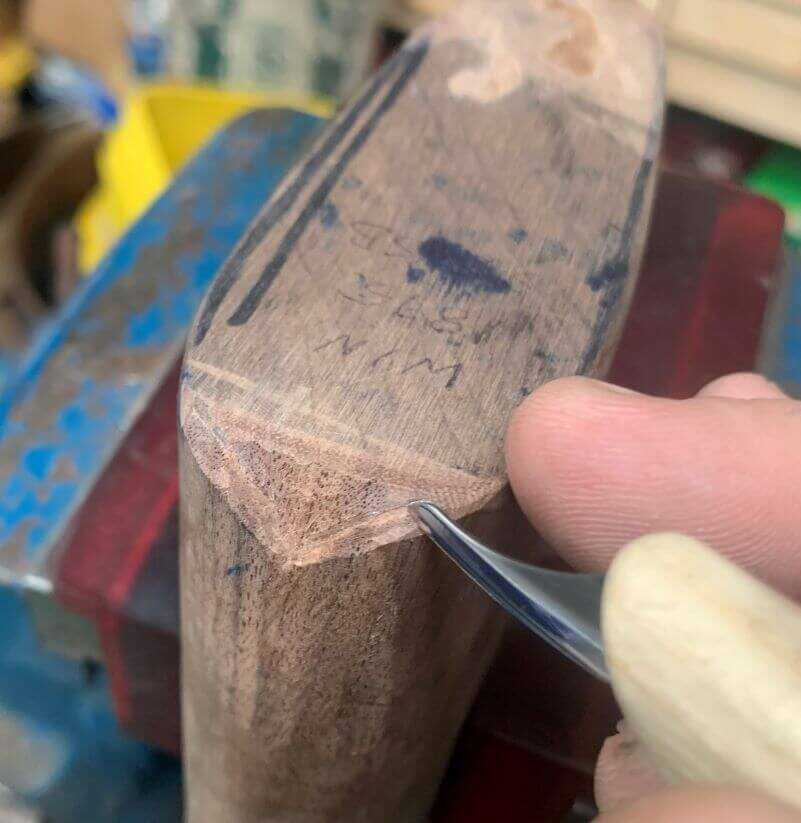
Along with the internal work, some external fitting and shaping were required as well. The stock needed to be cut for the buttplate. It is my understanding that Winchester 1895s had a few different types of buttplates during their production. And so the new stock was left without cutouts for the buttplate and I would have to add them. The buttplate on this rifle is rounded on top and comes to a point. After marking out where the point needed to be, I started carving it out with the palm chisel. Then I finished it up with the carving knife. The buttplate for this rifle is not flat, being curved towards the “inside”, so I used a large half-round file to contour the back of the stock to match this radius. It didn’t take a whole lot, but some work there was definitely necessary. With the stock fitted for the buttplate, I drilled the holes for the buttplate screws. Pay particular attention to the screw size, and their orientation when drilling these holes. Sometimes these screws don’t just go straight in from the back. Once the screw holes were drilled, I finished shaping the outside contour to match the buttplate.
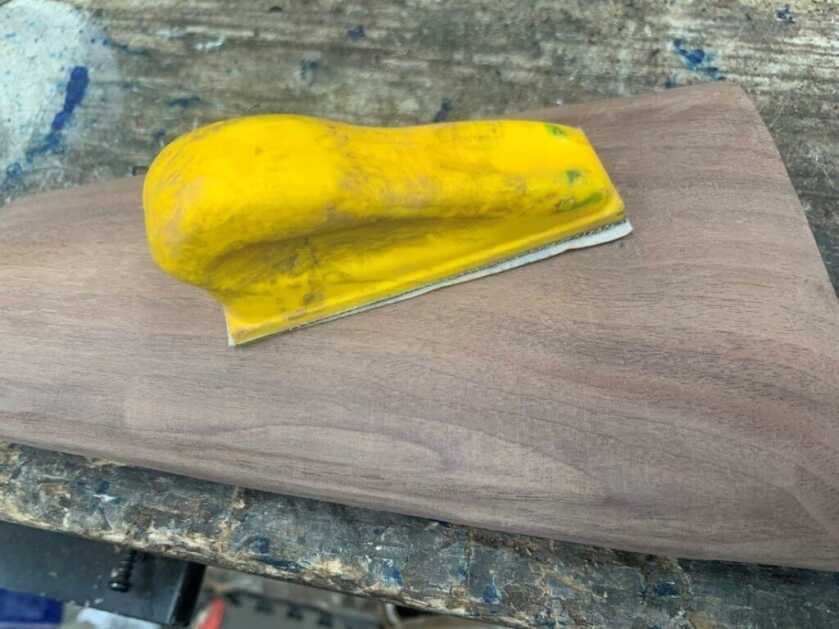
With the fitting and shaping done, it was time to prepare the surface for the finish. This process is a bit tedious. I started with coarse 80 grit sandpaper. I used a sanding block to ensure I didn’t round off any edges and to make the process easier. I sanded away the surface defects using this coarse paper. Now to be clear, for this particular project I didn’t remove all of them. The handguard on this rifle is original with 130 years of usage, wear, and light damage. A completely brand new stock lacking any blemishes would look a bit odd. So, I didn’t sand out all of the marks and defects. This sort of thing may be a consideration in your project as well. Anyway, I went to progressively finer grit sandpaper until I finished with the 320 grit sandpaper that the instructions had called for.
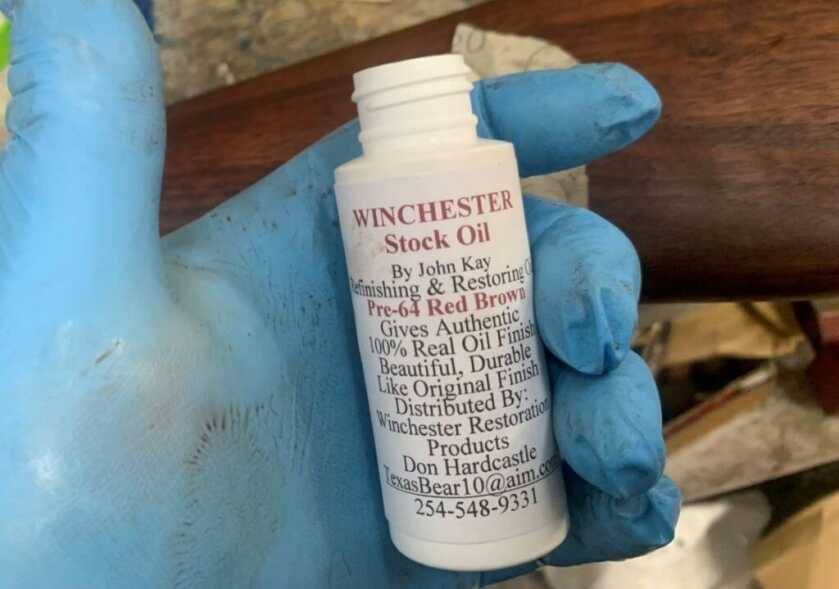
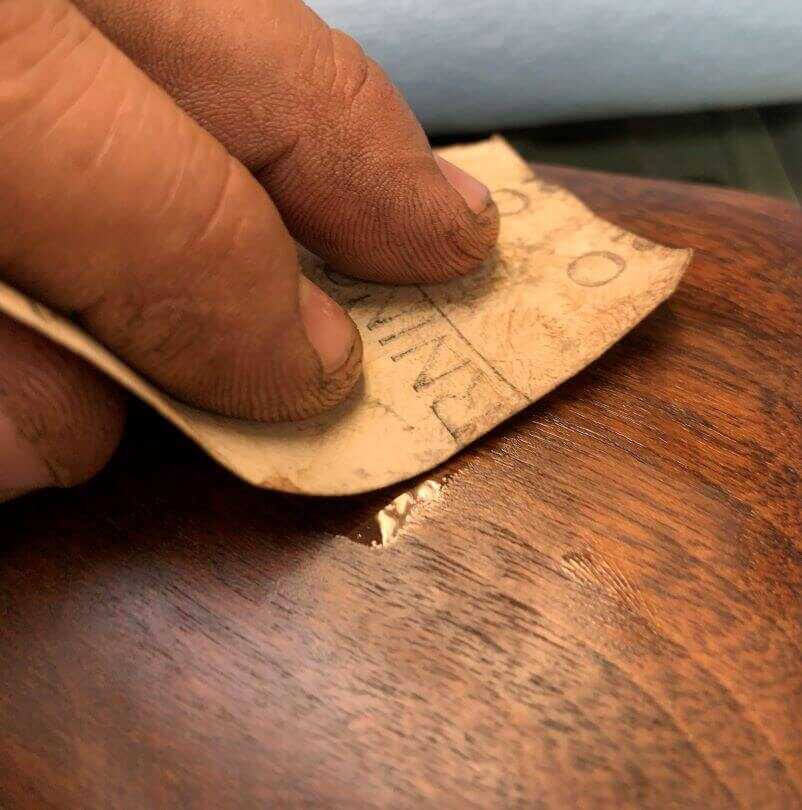
Mr. Pearce had asked for a specific finish that was supposed to recreate the original finish Winchester applied to them. This oil finish is mixed with mineral spirits to thin it. Then I used a wet sanding technique using this mixed oil. I put oil on 320 grit sandpaper and sanded the stock. The “wet sanding” significantly reduces the material removed by sanding. This also creates a type of paste that is then spread into the pores of the wood to fill them, which smoothes out the surface of the wood. I wiped the stock across the grain, to leave some in the grain. Then I left the stock to dry for a few days. I applied three coats and then I switched to 400 grit paper and repeated the process. Then it’s time for final finishing.
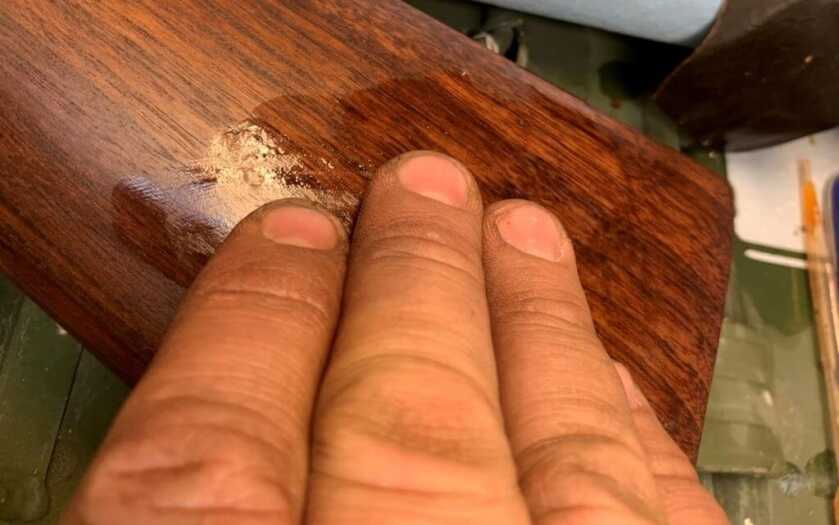
This particular finish calls for “hand-rubbed” final finishing. While I didn’t find it to be terribly labor-intensive, it is rather time-consuming. I applied just a little dab of the oil mixture and rubbed it in with my hand. Don’t use too much or you’ll end up with a sticky mess. I rubbed it until it started to feel a little warm, just like the instructions called for. Then after I had rubbed oil on all of the stock in this manner, I wiped off the excess with a rag and let it dry for 2-3 days. You may need to adjust this time based on your environmental conditions at the time. I repeated this process about 10 times. So it’s a few minutes of work, and then it has to sit for a few days. But by this point, it was looking pretty good. Then it was time to put everything back together.

Fitting and finishing a wood stock is a worthwhile skill set for a hobby gunsmith to have. After all, anything with a stock could need a replacement at some point in its life. Or you might just want to spruce up that broken old hunting rifle by replacing the wood furniture. Maybe you prefer the look and feel of a wood stock over a synthetic stock. In any case, fitting and finishing a wood stock is a very rewarding project. Until next time, Happy ‘Smithing!
Nice job. When I was working on guns I liked the metal work…but hated the wood working. I did do some decent stock work…but it was harder than most gunsmithing for me. After about 3 years I decided if I wanted to go blind I just poke eyes out with a knife rather than keep on checkering. Curved buttplates were the hardest for me. You did great